10 types of plastic resin and application
Short Description:
Plastic products are widely used, and there are many kinds of plastics found today. Let’s share with you the knowledge of 10 types of plastics resin and their application
To do well in the design and manufacture of plastic products, we must understand the types and uses of plastic.
Plastic is a kind of high molecular compound (macrolecules) which is polymerized by addition polymerization or polycondensation reaction with monomer as raw material. There are many kinds of plastics with different properties, but it is easy to be light in weight, easy to form, easy to obtain raw materials and low in price, especially the excellent corrosion resistance, insulation and heat preservation, impact resistance properties are widely used in industry and human life.
Characteristics of Plastics:
(1) The main components of plastic raw materials are polymer matrix called resin.
(2) Plastic has good insulation for electricity, heat and sound: electrical insulation, arc resistance, heat preservation, sound insulation, sound absorption, vibration absorption, excellent noise reduction performance.
(3) , good processability, through injection molding, can be made into products with complex shape, stable size and good quality in a very short time.
(4) Plastic raw material: it is a kind of material with polymer synthetic resin (polymer) as the main component, infiltrating into various auxiliary materials or some additives with specific use, having plasticity and fluidity under specific temperature and pressure, which can be molded into a certain shape and keep the shape unchanged under certain conditions..
Plastics classification
According to the molecular structure of synthetic resin, plastic raw materials mainly include thermoplastic and thermosetting plastics: for thermoplastic plastics, plastic materials that are still plastic after repeated heating are mainly PE / PP / PVC / PS / ABS / PMMA / POM / PC / PA and other common raw materials. Thermosetting plastic mainly refers to the plastic made by heating and hardening synthetic resin, such as some phenolic plastic and amino plastic. Polymer is composed of many small and simple molecules (monomer) by covalent bond.
1. Classification according to the characteristics of resin during heating and cooling
(1) Thermoset plastics: after heating, the molecular structure will be combined into a network shape. Once it is combined into a network polymer, it will not soften even after reheating, showing the so-called [irreversible change], which is caused by the change of molecular structure (chemical change).
(2) , thermoplastics: refers to the plastic that will melt after heating, flow to the mold for cooling and forming, and then melt after heating. It can be heated and cooled to produce [reversible change] (liquid ←→ solid), which is the so-called physical change.
A. General plastic: ABS,PVC.PS.PE
B. General engineering plastics: PA.PC,PBT,POM, PET
C. Super engineering plastics: PPS. LCP
According to the scope of application, there are mainly general plastics such as PE / PP / PVC / PS and engineering plastics such as ABS / POM / PC / PA. In addition, there are some special plastics, such as high temperature and humidity resistance, corrosion resistance and other plastics modified for special purposes.
2. Classification by use of plastics
(1) General plastic is a kind of widely used plastic. Its output is large, accounting for about three quarters of the total plastic output, and its price is low. It is widely used to make daily necessities with little stress, such as TV shell, telephone shell, plastic basin, plastic barrel, etc. It has a very close relationship with people and has become an important pillar of the plastic industry. Commonly used general plastics are PE, PVC, PS, PP, PF, UF, MF, etc.
(2) Engineering plastics Although the price of general plastics is low, its mechanical properties, temperature resistance and corrosion resistance are difficult to meet the needs of structural materials in some engineering and equipment. Therefore, engineering plastics came into being. It has high mechanical strength and rigidity, can replace some steel or non-ferrous materials, and can manufacture mechanical parts or engineering stress parts with complex structure, many of which are more effective than the original ones The common engineering plastics are PA, ABS, PSF, PTFE, POM and PC.
(3) Special plastic raw materials, which have unique functions, can be used in some special occasions, such as magnetic conducting plastics, ionomer plastics, pearlescent plastics, photosensitive plastics, medical plastics, etc.
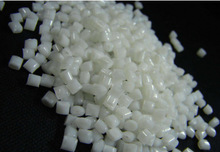
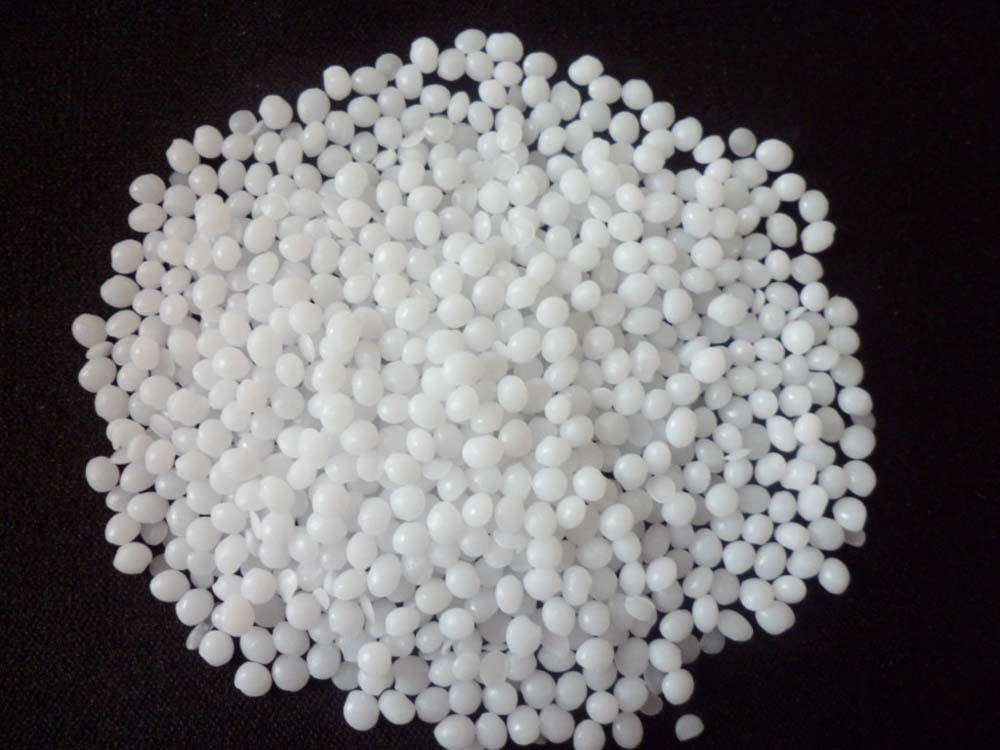
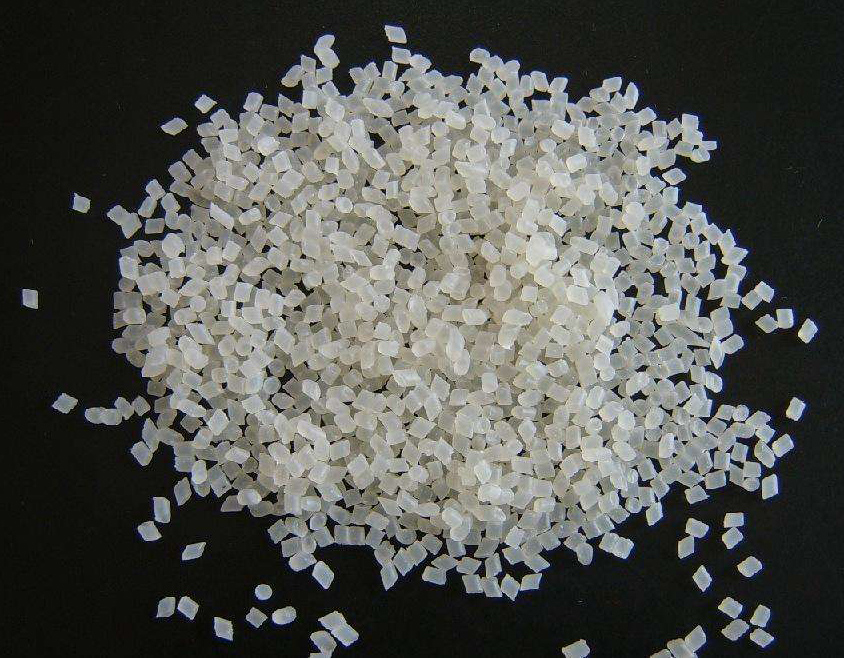
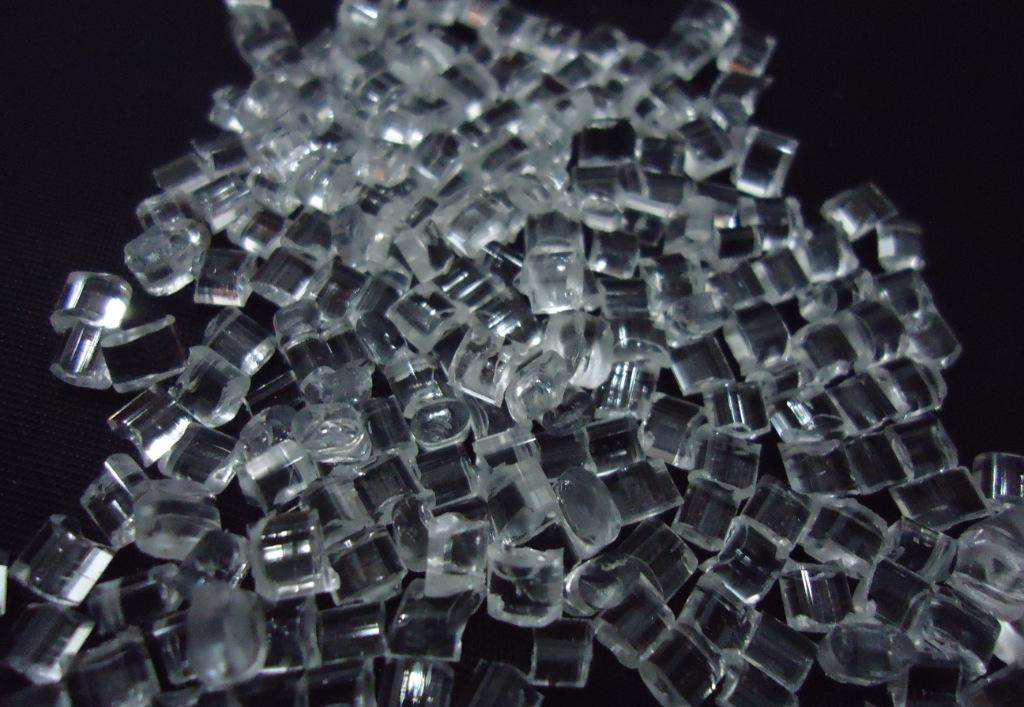
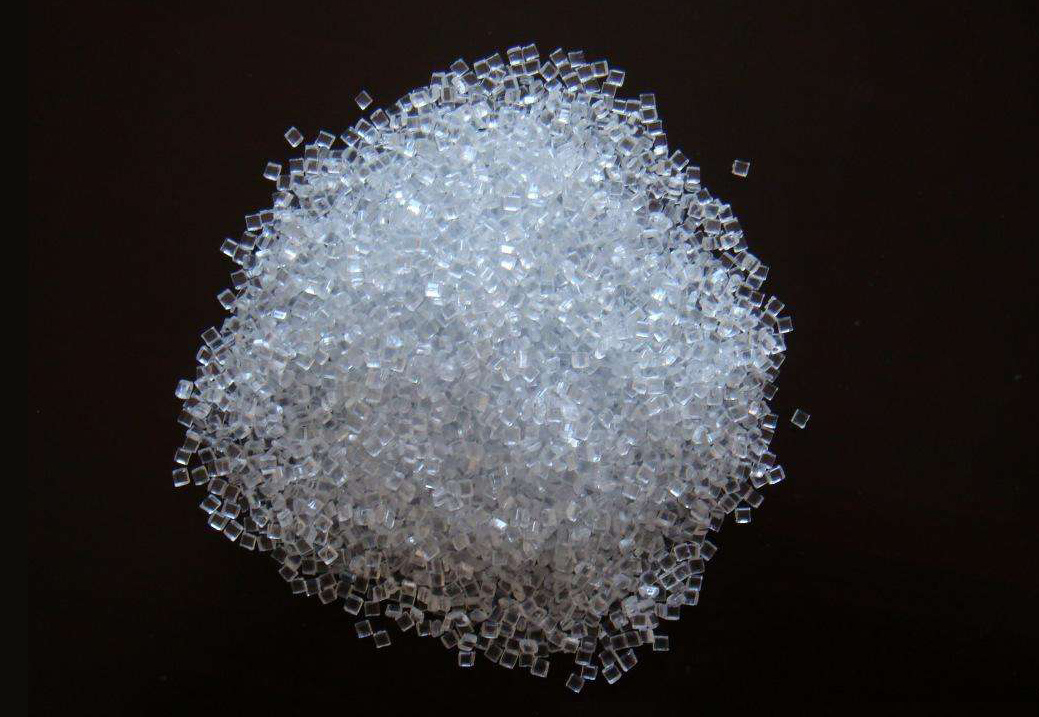
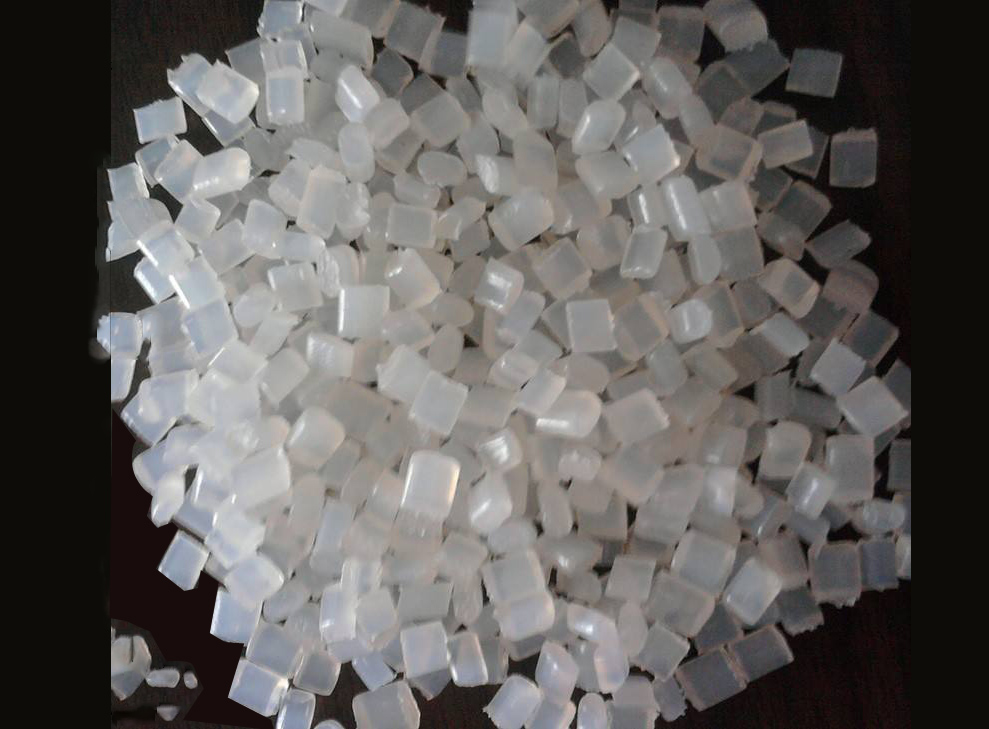
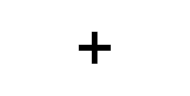
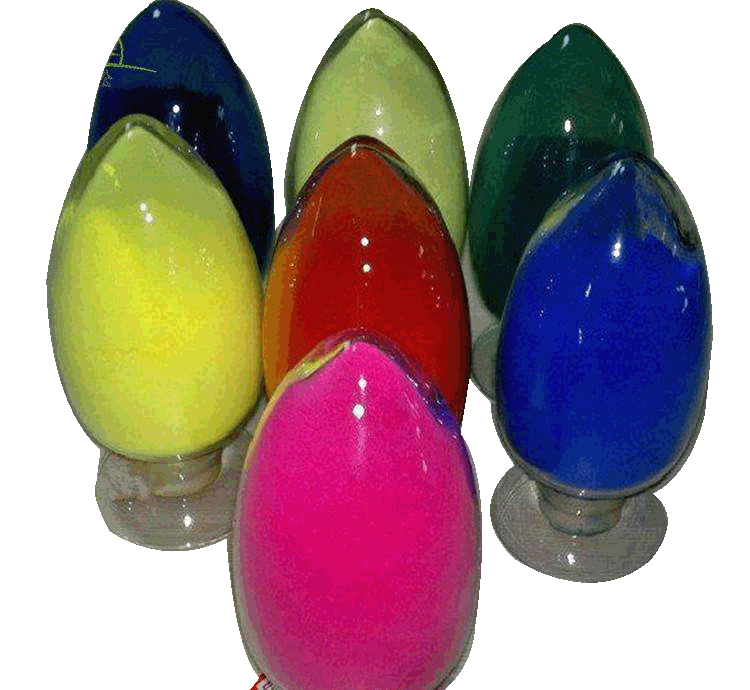
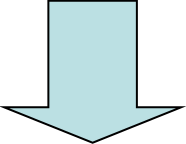
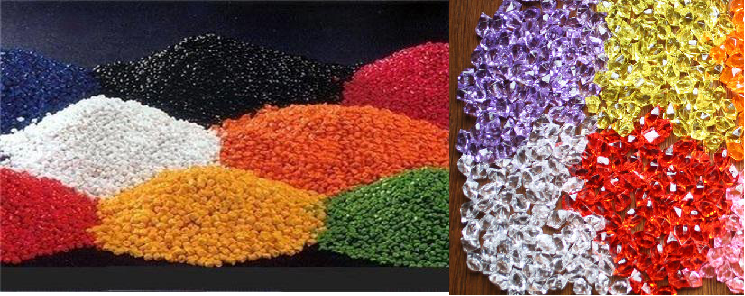
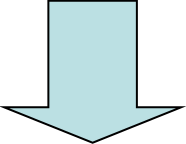
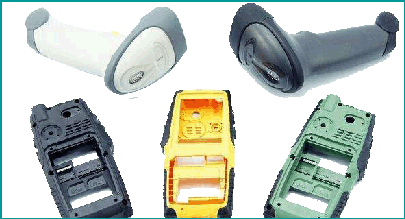
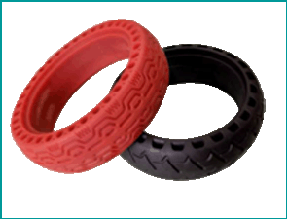
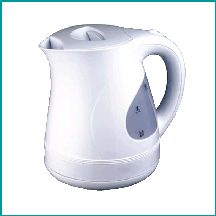
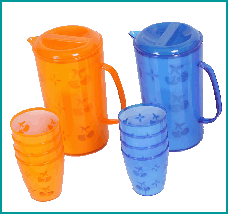
Molded into various parts
Application of 10 types plastics resins:
1. General plastics
(1).PP (polypropylene): the combustion has the smell of petroleum, the flame background color is blue; floating water.
Homopolymer PP: translucent, flammable, wire drawing, electrical appliances, board, daily products.
Copolymerized PP: natural color, flammable, electrical appliances, home appliances accessories, containers. Random copolymerization PP: highly transparent, flammable, medical devices, food containers, packaging products
(2).ABS (polystyrene butadiene propylene copolymer):high glossiness, burning smoke, aromatic taste; submerged water.
ABS raw materials: high toughness and strength, flammable; electrical shell, plate, tools, instruments .
ABS modification: increase rigidity and flame retardant, non combustible; auto parts, electrical parts
(3).PVC (polyvinyl chloride): smell of chlorine burning, green at the bottom of the flame; submerged water.
Rigid PVC: high strength and hardness, flame retardant; building materials, pipes .
Soft PVC: flexible and easy to process, hard to burn; toys, crafts, jewelry
2. Engineering plastics
(1).PC (polycarbonate): yellow flame, black smoke, special taste, submerged water; rigid, high transparency, flame-retardant; mobile digital, CD, led, daily necessities.
(2).PC / ABS (alloy): special fragrance, yellow black smoke, submerged water; rigid toughness, white, flame-retardant; electrical materials, tool case, communication equipment.
(3).PA (polyamide PA6, PA66): slow nature, yellow smoke, burning smell of hair; toughness, high strength, flame retardant; equipment, mechanical parts, electrical parts.
(4).POM (polyformaldehyde): burning tip yellow, lower end blue, formaldehyde odor; toughness, high strength, flammable; gear, mechanical parts.
(5).PMMA (polymethyl methacrylate); special pungent taste: high light transmittance; plexiglass, handicrafts, ornaments, packaging, film compliance .
3. Elastomer plastic
(1).TPU (polyurethane): special taste; good elasticity, toughness and wear resistance, flammable; mechanical parts, electronic parts .
(2).TPE: special fragrance, yellow flame; SEBS modified, physical hardness adjustable, good chemical property, flammable; toys, secondary injection handle, handlebar bags, cables, auto parts, sports equipment
There are four kinds of plastic molding technology: injection molding, extrusion molding, calendering molding and molding. Injection molding is the main process to obtain complex structure and precision size plastic parts. Injection production needs to rely on three elements of injection mold, injection machine and plastic raw materials to complete the system. Mestech focuses on plastic injection mold manufacturing and plastic parts molding for more than 10 years, and has accumulated rich technology and experience. We are dedicated to provide you with mold manufacturing and plastic parts molding services, please contact us.