Automobile lampshade injection molding
Short Description:
Plastic injection molding is generally used for automobile lampshade. Lamp is an important component of automobile. Automobile lampshade is one of the most precise injection molding parts in automobile. The automobile lampshade injection molding is very important
The lamps are important components in an automobile . Automobile lampshade is one of the most precise injection molding parts in automobiles. Injection molding of automobile lampshade has special significance.
The lamp is the signal, illumination and indication system on the automobile, and it is an important system on the automobile. Outside the LED wick, the lampshade, lamp holder and housing are all injection moulded parts.
Nowadays, the automobile manufacturing industry is highly developed. The shape of the lamp matches the shape of the whole automobile, and emphasizes the beautiful and delicate appearance. This kind of complex shape lampshade can not be made with glass material. The emergence of new plastic polycarbonate PC (polycarbonate) meets the requirements of light transmission, strength, toughness and weather resistance. So PC injection molding automobile lampshade is widely used in automobile industry.
Lamp holder and lamp housing are not exterior parts. Generally PP + TD20 is used, which requires lower requirements than lamp shade. There is no focus here.
Automobile lamps basically includes the following types:
Head lamps
Tail lamps
Parking lamps
Fog lamps
Side marker lamps
3RD brake lamps
Roof lamps
Door mirrior lamps
Spot lamps
Auxiliary lamps
Day time running lamps
Back-up/revise lamps
Automotive lights for truck
Automotive lights for motorcycles
Automobile Lamps and Plastic Parts
The automobile lamp itself is complex in shape, exquisite in appearance, and has been exposed for a long time. Especially, the injection pressure time of some high-grade lamp shade moulds is very high. At the same time, the lamp shade has been exposed for a long time. Color powder for injection molding, high grade transparent powder for good light transmission. Polycarbonate has high hardness, high strength, high toughness, good anti-ultraviolet light transmission, anti-aging impact, so the lampshade still keeps good color transparency and mechanical strength after long use.
*Two tips you need to know about automobile lampshade design and mold design
1).Automobile lampshade is a very precise part. It has high requirements on assembly size, appearance shape, surface quality and optical characteristics. This has high requirements for lampshade design, material selection, die material structure, molding technology and injection technology. In the die design, the structure design of automobile lampshade must be analyzed by moldflow, and the structure should be optimized to avoid shrinkage, clamping and deformation caused by thickness change and unreasonable structure.
2).The injection mould of lampshade must adopt the steel with stable size, high hardness, wear resistance and corrosion resistance, and carry out hardening treatment and mirror finishing. Hot runner or hot runner system is used for gumming of injection moulds to eliminate injection defects such as temperature, fusion line and stress deformation.
Why we choose PC to make automobile lampshades
Almost all automobile lampshades are made of PC injection molding. PC plastics have good transparency, good strength and toughness, and better anti-ultraviolet ability than acrylic, not easy to aging, yellowing and fading.
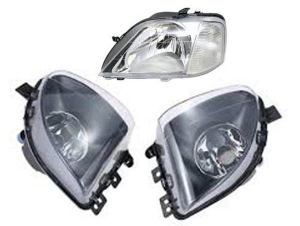
Pair of car fog lamp lampshade
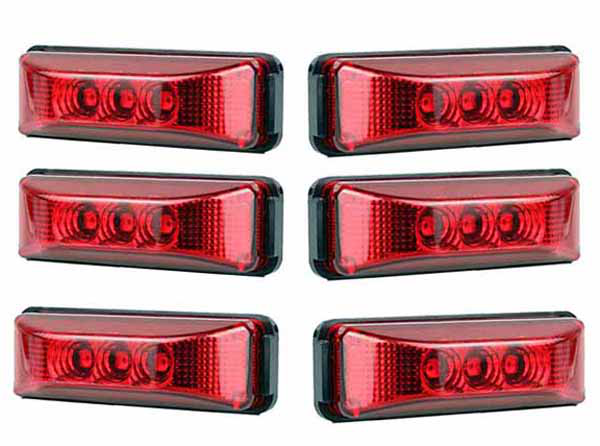
Automobile side marker lamp
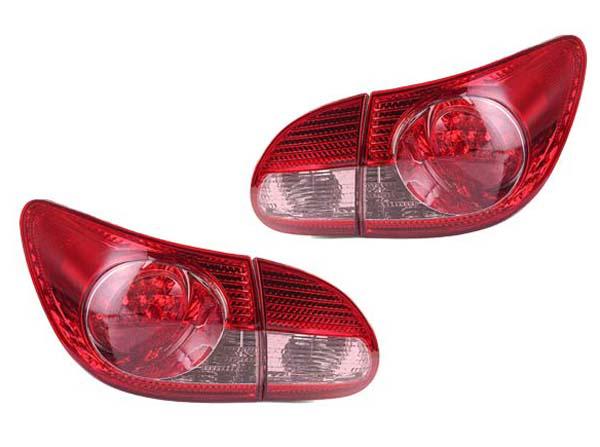
Automobile tail lampshade
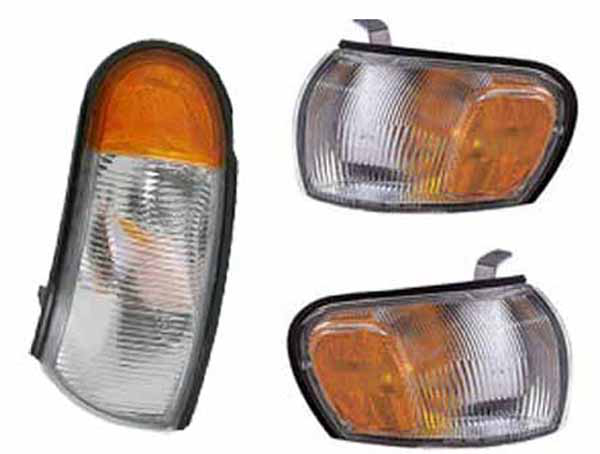
Automobile parking lampshade
*Six tips you need to know about injection molding of automobile lampshade
1). Special injection molding machine is recommended for automotive lampshade. If several materials or colors are shared, clean the injection molding machine until the pure color comes out. At least 25KG raw material is required.
2). Injection molding machine is best sealed, dust and sundries into the mould, causing scratches and foreign bodies, black spots are very troublesome, and the mould polishing is also troublesome.
3). PC has strong electrostatic adsorption, so it needs to be equipped with an electrostatic gun to eliminate electrostatic.
4). The choice of antirust agent and cleaner for mould is very important. Do not choose oily, choose dry
5). PC materials need to choose the brand of fluidity and color stability.
6). PC needs dehumidification and drying, 120 degrees for 4 hours.
*Surface treatment of automobile plastic lampshades:
There are two main surface processes of automobile lamps vacuum aluminizing and surface spraying.
1). Plating a layer of aluminum on the surface of plastic parts can not only give the plastic parts a certain metal texture, but also reflect the light emitted by the light source like a mirror. Therefore, in the automotive lamp manufacturing industry, the application of vacuum aluminum plating is very common.
2). Surface spraying: mainly for the surface treatment of automobile headlamp cover.
① Harden paint: most of the automobile headlamp covers are made of PC materials. The surface of PC lampshade is very soft after molding, and obvious traces can be left by fingernails. After spraying a layer of harden paint on the outer surface of PC lampshade, the surface is hard and can avoid those slight scratches.
② Antifogging coating: the purpose of spraying antifogging coating inside the lampshade is to increase the tension of the inner surface of the lampshade, turn the small water droplets into a layer of water film, reduce the divergence of light and reduce the influence of fog on the light distribution of lamps.
Mestech have been devoting ourselves to the design, manufacture and injection moulding of automobile lamps and other related parts for many years. Please contact us.
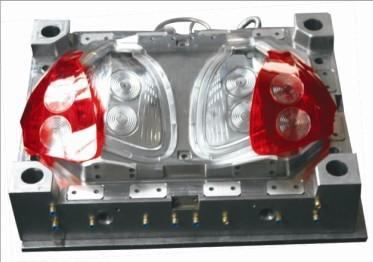
Mold for tail lamp shade
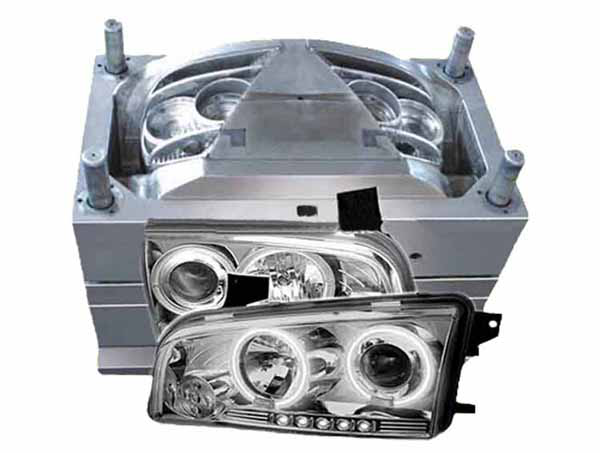