China OEM Microplast Injection Molding Machine Suppliers - Plastic electroplating and vacuum plating – Mestech
Short Description:
China OEM Microplast Injection Molding Machine Suppliers - Plastic electroplating and vacuum plating – Mestech Detail:
Compared with spraying paint, plastic electroplating and vacuum plating has better wear resistance, corrosion resistance and unique metallic luster. It is commonly used in some high-end product parts, such as multimedia product housings, smart watch cases, buttons, lamp holders, lampshades and decorations.
The principles of water electroplating and vacuum plating are different, and the applicable objects and the results are different. Let’s introduce below:
1. Plastic electroplating
Plastic electroplating is the process of immersing plastic parts in electrolyte and depositing metal particles on the surface of work-piece by loading current or chemical reaction. After electroplating, the surface color is silver, sub silver and silver gray.
The ABS plastics were pretreated by silver nitrate chemical copper process, colloidal palladium PD chemical nickel direct plating to produce a conductive layer with good adhesion on its surface, and then other metals were electroplated.
Electroplating is done in electrolytic water solution, so it is called “water electroplating”, “hydropower plating”. More common are copper plating on the surface of plastic, nickel chromium, trivalent chromium, gun color, pearl nickel and so on.
In theory, all plastics can be electroplated, but at present only ABS, ABS + PC are the most successful, but the adhesion of electroplated coating on other plastics is not satisfied. The process of water electroplating is simple and does not need to spray primer before and after plating. The coating has good adhesion, thick coating and low cost.
2. Plastic vacuum plating (Physical Vapour Deposition-PVD)
Vacuum plating mainly includes vacuum evaporation, sputtering and ion plating. They all deposit various metal and non-metal films on the surface of plastic
parts by distillation or sputtering under vacuum. In this way, a very thin surface coating can be obtained.
Vacuum plating mainly includes vacuum evaporation plating, sputtering plating and ion plating. They are all used to deposit various metals on the surface of plastic parts by distillation or sputtering under vacuum conditions.
Non-metallic film, through this way can be very thin surface coating, and has the outstanding advantages of fast speed and good adhesion, but the price is also higher, generally used for comparison, functional coatings for high-end coating can products.
Vacuum be used in plastics such as ABS, PE, PP, PVC, PA, PC, PMMA, etc. Thin coatings can be obtained by vacuum plating.
Vacuum coating materials can be plated with a variety of metals, such as aluminum, silver, copper and gold, which have lower melting point than tungsten wire.
3. Plastic vacuum plating (Physical Vapour Deposition-PVD)
Vacuum plating mainly includes vacuum evaporation, sputtering and ion plating. They all deposit various metal and non-metal films on the surface of plastic
parts by distillation or sputtering under vacuum. In this way, a very thin surface coating can be obtained.
Vacuum plating mainly includes vacuum evaporation plating, sputtering plating and ion plating. They are all used to deposit various metals on the surface of plastic parts by distillation or sputtering under vacuum conditions.
Non-metallic film, through this way can be very thin surface coating, and has the outstanding advantages of fast speed and good adhesion, but the price is also higher, generally used for comparison, functional coatings for high-end coating can products.
Vacuum be used in plastics such as ABS, PE, PP, PVC, PA, PC, PMMA, etc. Thin coatings can be obtained by vacuum plating.
Vacuum coating materials can be plated with a variety of metals, such as aluminum, silver, copper and gold, which have lower melting point than tungsten wire.
What is the difference between plastic electroplating and plastic vacuum plating ?
(1)Vacuum plating is a process of coating in spraying line and vacuum furnace, while electroplating is a process in aqueous solution. Because it is spraying paint, vacuum plating is not suitable for complex shape products, while water electroplating is not restricted by shape.
(2) Processing technology, such as vacuum coating of plastic glue, can be summarized simply: basic surface degreasing, dedusting, electrostatic precipitation, spraying UV primer, UV curing, vacuum coating, dedusting, spraying surface bottom (color concentrate can be added), curing, finished products; vacuum coating is limited by process, and it is not suitable to process products with too large area because of work. The art process is not well controlled, and the rate of defects is high.
Plastic electroplating (generally ABS, PC/ABS): chemical deoiling hydrophilic coarsening reduction preimpregnation palladium activation acceleration electroless nickel plating hydrochloric acid activation coke copper sulfuric acid activation semi-bright nickel nickel sealing chromium plating drying finished products;
(3) Electricity plating can be completed in fully automated production.
(4) as far as appearance is concerned, the color brightness of vacuum aluminized film is brighter than that of electroplating chromium.
(5) As far as performance is concerned, plastic vacuum coating is the outermost layer of paint, while water electroplating is usually metal chromium, so the hardness of metal is higher than that of resin.
s for corrosion resistance, paint coating is usually used. Cover layer is better than metal layer, but there is little difference between them in high-end product requirements; in weathering, electroplating is better than vacuum plating, so it usually needs long-term outdoor use with weather resistance.
In the automotive industry, there are also strict requirements for resistance to high bottom temperature, humidity and heat, solvent wiping and so on.
(6) Vacuum plating is mainly used in the electronic communication industry, such as mobile phone shell, automotive applications, such as reflective cups of automotive lamps; water plating is mainly used for decorative chromium, such as automotive door trim. Door knobs and so on.
(7) In terms of product appearance color diversity, vacuum plating is richer than electroplating. Vacuum plating can be made into gold and other color surfaces.
(8) as far as processing cost is concerned, the current vacuum plating cost is higher than that of water plating.
(9) Vacuum plating is a green environmental protection process with rapid technological development, while water electroplating is a traditional process with high pollution, and the industry is limited by the influence of national policies.
(10) Here is a spraying process (silver mirror reaction) which has just emerged. The process is plastic degreasing and deelectrostatic special primer baking nano-spraying pure water baking.
This technology can also make mirror effect on plastic surface. It is also an environmentally friendly process. The former and the latter processes are the same as vacuum plating, but only the middle plating.
Aluminum is replaced by silver-sprayed mirror, but the current technical performance of this process can not be compared with water plating and vacuum plating. It can only be applied to handicraft products which do not require high appearance and performance.
Production line
If your have products with electroplated plastic parts or vacuum plated plastic parts please contact us.
Product detail pictures:




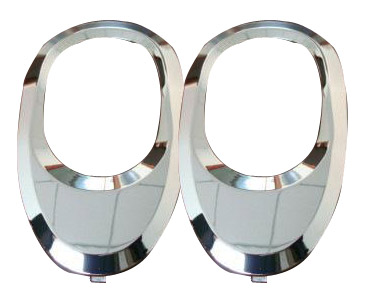



Related Product Guide:
Cooperation
We depend on sturdy technical force and continually create sophisticated technologies to meet the demand of China OEM Microplast Injection Molding Machine Suppliers - Plastic electroplating and vacuum plating – Mestech, The product will supply to all over the world, such as: Guinea, Gambia, Japan, we rely on own advantages to build a mutual-benefit commerce mechanism with our cooperative partners. As a result, we have gained a global sales network reaching the Middle East, Turkey, Malaysia and Vietnamese.

Customer service staff and sales man are very patience and they all good at English, product's arrival is also very timely, a good supplier.
