Die casting process
Short Description:
Die casting process is the process in which zinc, copper, aluminum, magnesium, lead, tin and lead tin alloys and their alloys are melted at high temperature and injected into the mold cavity, and then cooled under pressure to obtain parts.
The working temperature of non-ferrous metal die casting is much lower than that of iron casting, and the corresponding foundry equipment and process requirements are simple, and small. Die casting production can obtain very good surface quality and dimensional accuracy, especially suitable for large-scale standard manufacturing of small and medium-sized parts, which provides a good part support for modern electronics, electrical appliances, automobiles, medical devices, instruments and kithen tools. Different metal alloys have much different character in die casting process. Their minimum section and minimum draft are different, melt point temperature are different, surface finish are different, So it is best to involve our team of engineers early on during the design process to utilize our expertise with design for manufacturing.
There are five main factors in metal die casting process :
1.Die casting material;
2.Types of Die casting Process;
3.Die casting machine;
4.Die casting mold;
5.Post Processing and Finishing for Die Casting Parts
Metal die casting process is a process of unifying the pressure, speed and time by using the three elements of machine, mould and alloy. For metal hot working, the existence of pressure is the main characteristic of die casting process which is different from other casting methods. Pressure casting is a special casting method with less and no cutting, which has developed rapidly in modern metal processing technology. It is a process of filling the mold with molten metal under high pressure and high speed, and forming the casting by crystallization and solidification under high pressure. High pressure and high speed are the main characteristics of die casting. The commonly used pressure is tens of megapascals, filling speed (inner gate speed) is about 16-80m / s, and the filling time of metal liquid in mold cavity is very short, about 0.01-0.2s. Metal die casting is a metal casting process that is characterized by forcing molten metal under high pressure into a mold cavity. The mold cavity and core is made using harden steel dies which have been machined into shape and work similarly to an injection mold during the process. Depending on the type of metal being cast, a hot- or cold-chamber machine is used.
1.Die casting materialMESTECH provides die casting parts for zinc alloy, aluminum alloy and magnesium alloy. Because these three materials are the most widely used die casting alloy materials at present.
Zinc alloy characteristics:
---High strength and hardness
---Excellent electrical conductivity
---High thermal conductivity
---Low cost raw material
---High dimensional accuracy and stability
---Excellent thin wall capability
---Ability to cold form, which eases joining
---High quality finishing characteristics
---Outstanding corrosion resistance ---Full recyclability
2.Aluminum Alloy Characteristics:
---High operating temperatures
---Outstanding corrosion resistance
---Lightweight
---Very good strength and hardness
---Good stiffness and strength-to-weight ratio
---Excellent EMI and RFI shielding properties
---Excellent thermal conductivity
---High electrical conductivity
---Good finishing characteristics
---Full recyclability
3. Magnesium Alloy Characteristics:
---High conductivity; electrical, and thermal
---Withstands high operating temperatures
---High dimensional accuracy and stability
---Exceptional thin wall capability
---Good environmental corrosion resistance
---Good finishing characteristics
---Full recyclability
1 The Hot-Chamber Die Casting Process
Hot-chamber die casting, sometimes called gooseneck casting, is the more popular of the two die casting processes. In this process, the cylinder chamber of the injection mechanism is completely immersed in the molten metal bath. A gooseneck metal feed system draws the molten metal into the die cavity.
While direct immersion in the molten bath allows for quick and convenient mold injection, it also results in increased corrosion susceptibility. Due to this fact, the hot-chamber die casting process is best suited for applications that utilize metals with low melting points and high fluidity. Good metals for the hot-chamber die casting process include lead, magnesium, zinc and copper.
2 The Cold-Chamber Die Casting Process
The cold-chamber die casting process is very similar to hot-chamber die casting. With a design that focuses on minimizing machine corrosion rather than production efficiency, the melted metal is automatically- or hand-ladled into the injection system. This eliminates the necessity for the injection mechanism to be immersed in the molten metal bath.
For applications that are too corrosive for the immersion design of hot-chamber die casting, the cold-chamber process can be an excellent alternative. These applications include the casting of metals with high melting temperatures, such as aluminum and aluminum alloys.
3 The Low-Pressure Die Casting Process
Low-pressure die casting is a process best suited for aluminum components that are symmetric around an axis of rotation. Vehicle wheels, for example, are often fabricated through low-pressure die casting. In this type of process, the mold is situated vertically above the molten metal bath and connected via a riser tube. When the chamber is pressurized (usually between 20 and 100kPa), the metal is pulled upward and into the mold. The elimination of feeders from this type of die casting process delivers the high casting yields.
4 The Vacuum Die Casting Process
Vacuum pressure casting (VPC) is a relatively new die casting process that delivers enhanced strength and minimal porosity. This process is similar to low-pressure die casting, except the locations of the die cast mold and molten metal bath are reversed. The cylinder chamber can become a vacuum, which forces the molten metal into the mold cavity. This design reduces turbulence and limits the amount of gas inclusions. Vacuum die casting is especially beneficial in applications destined for post-casting heat treatment.
5 The Squeeze Die Casting Process
Squeeze casting was created as a workable solution for casting metals and alloys with low fluidity. In this process, the molten metal fills up an open die, which then squeezes closed, forcing the metal into the recessed portions of the molding. The squeeze casting process delivers extremely dense products and is a complementary process to subsequent heat-treating. The process is most often associated with molten aluminum, and is used in applications that call for fiber reinforcement.
6 The Semi-Solid Die Casting Process
Semi-solid die casting, sometimes called Thixoforming, is another process that delivers minimal porosity and maximum density. A machine cuts the workpiece into smaller slugs, and then heated. Once the metal has reached the phase transition between solid and liquid, resulting in a somewhat slushy texture, a shot sleeve forces it into the mold cavity, where it hardens. The benefit of this is improved precision. Non-ferrous metals such as magnesium alloy and aluminum alloy are most often used with the semi-solid die casting process.
7.Types of Die casting Process
All die casting process types are designed with the same goal in mind—cast a mold using injected molten metal. Depending on the type of melted metal, part geometry and part size, different die casting processes can deliver superior results over alternative methods. The two main types of die casting processes are hot-chamber and cold-chamber die casting. Variations on these two types of die casting include:
Low-pressure die casting
Vacuum die casting
Squeeze die casting
Semi-solid die casting
1 Hot pressure chamber die casting machine
According to the structure and layout of the chamber, it can be divided into horizontal and vertical forms. The crucible for molten metal is attached to the machine by hot pressing chamber, and the piston mechanism for metal hydraulic pressure entering the mold is installed in the crucible. Some hot pressing chamber die casters use compressed air to directly inject metal hydraulic pressure into the mold without piston mechanism.
Hot chamber die casting machine
The hot pressing chamber die casting machine is mainly used for die-casting alloy with low melting point, such as zinc,Magnesium and tin.
2 Cold pressure chamber die casting machine
Melting the metal outside the machine and then adding the liquid metal into the compression chamber with a spoon can be divided into vertical cold chamber die casting machine and horizontal cold chamber die casting machine according to the direction of motion of the compression piston.
The liquid metal is removed from the furnace of the vertical cold press chamber die casting machine and poured into the compression chamber. The metal is hydraulic pressed into the mold by the compression piston, and the surplus metal is pushed out by another piston.
Cold chamber die casting machine
Cold chamber die casting machine
The horizontal cold chamber die casting machine is the same as the vertical one, but the piston movement is horizontal. Most modern die casting machines are horizontal. Cold-chamber die-casting machines can die-cast high melting point metals or easily oxidized metals, such as aluminum, copper alloys, etc.
3.Die casting machine.
Die casting machine is used for pressure casting machine. It includes two kinds of hot pressing chamber die casting machine and cold pressing chamber die casting machine. The cold pressing chamber die casting machine is divided into two types: straight and horizontal. The molten metal is injected into the mold by the die-casting machine under the action of pressure for cooling and forming, and the solid metal castings can be obtained after the mold is opened.
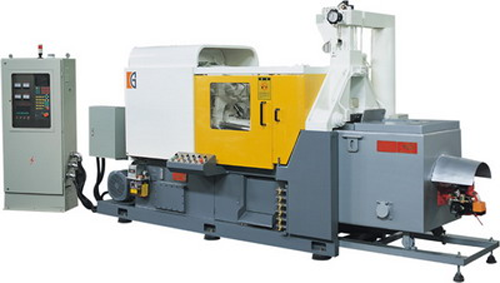
Hot chamber die casting machine
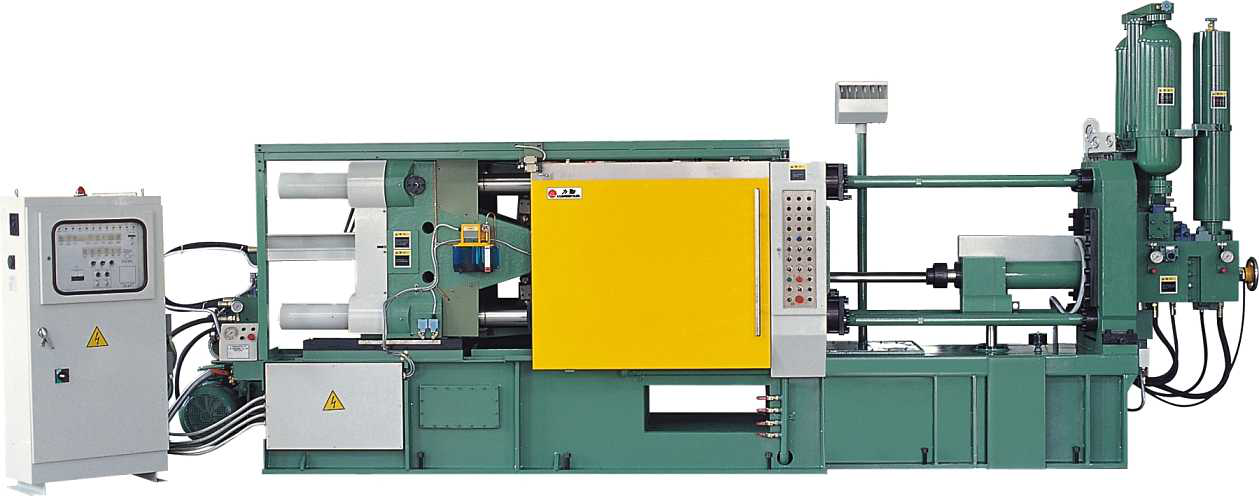
Cold chamber die casting machine
4.Die casting mold
In various molds, the working conditions of die casting die are rather harsh. Die casting is to make the molten metal filled with mold cavity under high pressure and high speed, and contact with hot metal repeatedly during the working process. Therefore, die casting mold is required to have high thermal fatigue resistance, thermal conductivity and wear resistance, corrosion resistance, impact toughness, red hardness, good demoulding and so on. Therefore, the surface treatment technology of die casting die requires high technology.
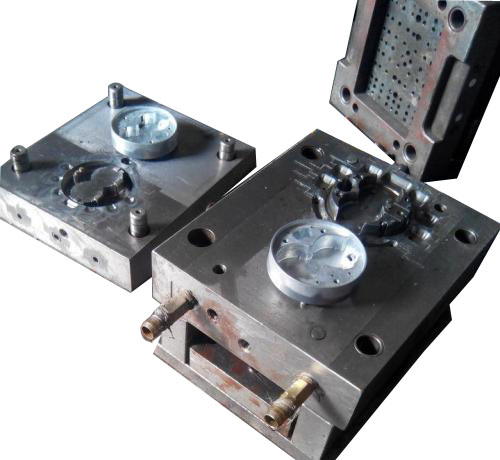
Die casting mold
5.Post Processing and Finishing for Die Casting Parts
We offer most post processing and finishing services for die cast parts from our select partners:
Services
CNC machining - vertical, horizontal, turning, 5-axis
Powder Coating
Liquid Coating
EMI - RFI Shielding
Plating - chrome, copper, zinc, nickel, tin, gold
Anodizing, Electrical Coating, Chromating/Non-chromating
Heat Treatment, Passivation, Tumbling
Graphics
In-house Artwork Process
Silk Screening
Pad Printing
Bead Blasting
Light Mechanical Assembly, including stud and helicoil inserts, O-ring, gasket
Laser Cutting and Engraving
Etching
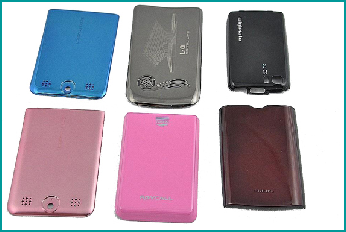
Electrical Coating & Silk Screening
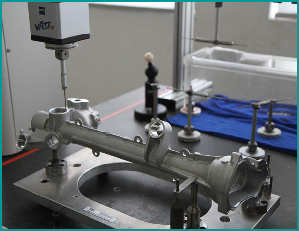