Mold design
Short Description:
Mold design is that engineers use professional knowledge and experience to conceive the mold for mass production of specific parts, and draw the process of mold construction with the aid of computer and drawing software.
Mold (mould) manufacturing starts with the mold design . Mold design is very important for mold manufacturing, because the mould is made strictly according to the drawings designed by engineers. The quality of mold design determines the cost and success of mold. it is also very important for the quality and efficiency of injection production.
1.Mission of mold design
In this stage, the work is to determine the dimensions, specifications, materials and layout of the internal components and subsystems of the mold. Mold design needs to consider the applicable scope, process type, mold material, quality system, main processing equipment, object of action, material, processing capacity, mold installation mode and other factors
In this stage, the precise design of each part of the mold is carried out. Review and modify the mold until it can be put into normal injection production.
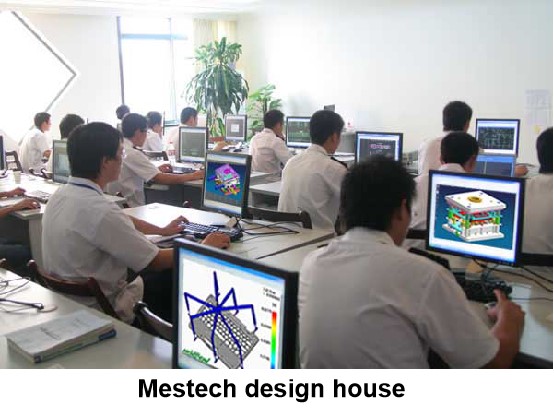
2.The flow of designing a mold
The mold is called "the king of tools",It means that the mould has high productivity in injection moulding and manufacturing accuracy, which is suitable for the requirements of modern mass production. Therefore, it is widely used in modern manufacturing. The structure of molds usually is precise and complex, much like a machine without power. Mold has complex mechanism and precision requirements, and the price is high. The size, accuracy and structure of the products are varied, and there are many kinds of materials. Injection mold working in high temperature environment requires high stability and service life. Designing a mold should follow the flow as below:
1. Review products design: To check if the product design has obvious problem with mold making. Such as: draft check, undercut check, thin wall and moldflow check
2. Layout design: Includes moldbase choose, insert material choose. gate position choose, parting-line design...... In this stage, the work is to determine the dimensions, specifications, materials and layout of the internal parts and subsystems of the mould
3. Detail design: Includes mechanism design, slider design, cool system design...... In this stage, completely design every part
4. Output 3D design for CNC programming, manufacturing documents
5. Follow up mold tooling, test-shot, estimate and modify the mould until it can be put into normal injection production.
3 The types of molds
The common classification of molds is
1 Hardware mold includes: stamping die (such as punching die, bending die, drawing die, turning die, shrinkage die, relief die, bulging die, shaping die, etc.), forging die (such as die forging die, upsetting die, etc.), extrusion die, extrusion die, die casting die, forging die, etc;
2 Nonmetal mold is divided into plastic mold and inorganic nonmetal mold. Our company mainly makes injection mold, metal die-casting mold and stamping mold
4.Experienced engineers and effective software tools
---Mold designers, in addition to being able to use software to design mold parts, also need to have a clear understanding of product design, material characteristics, mold steel, injection molding process. Mold designers of Mestech, generally have more than 5 years of mold design experience, can use MOLDFLOW and other software and their own experience to analyze and optimize the design for customers at a reasonable cost to design a successful mold. A mold is a hollow unit into which molten material is poured to form a casting. Mold design is the analysis, design, and refinement of molds for industrial manufacturing. Molds must be able to form the solid part out of the molten material, cool the part so it can solidify, and eject the part from the mold. The list of ways in which a mold can fail to accomplish these purposes is long and vivid. It's not surprising that mold design has a critical impact on the cost-effectiveness and quality of molded parts and thus of your product. A bad mold can give you that sinking feeling in more ways than one.
---Software for mold design: the tool for engineers to design mold is computer and design software. Different countries and regions in the world use different mold design software. At present, the following software is used in mold design:
1. Unigraphics (UG) is the most advanced CAD / CAE / CAM high-end software for manufacturing industry in the world. UG software is used by many of the world's leading manufacturers in various fields such as industrial design, detailed mechanical design and engineering manufacturing
2. Pro / E is the most popular 3D CAD / CAM system in the world. Widely used in electronics, machinery, mold, industrial design and toy industries. It integrates part design, product assembly, mold development and numerical control processing.
3. The most distinctive feature of CATIA is its powerful surface function, which can't be compared with any CAD 3D software. Now, CATIA is used by almost all airlines. The software covers all aspects of product design: CAD, CAE and cam. Software "Tool Design Extension" creates the most complex single-cavity and multi-cavity molds and casts with ease. Evaluate mold draft, undercut and thickness problems, and then automatically create parting surface and splitting geometry in a process-driven environment that’s simple–even for the occasional user–who needs to create complex tooling quickly. Software "Expert Moldbase Extension" gives you a familiar 2D environment for moldbase layout–and get all the benefits of 3D! The 2D process-driven GUI offers a catalog of standard and custom components, and updates your model automatically during the development of the moldbase, by providing a catalog of standard and customized components. Your resulting 3D models are then used for interference checking during mold opening, as well as automatic generation of deliverables such as detail drawings and BOMs.
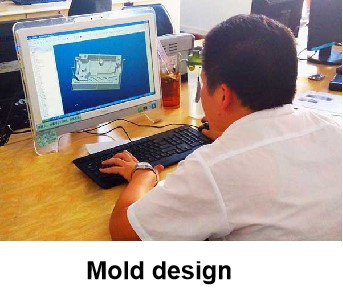

5.Analysis and verification during mold design
1. Failure mode analysis on product parts DFMEA (Failure mode analysis )is very important before mold design. Before mold design begins, DFMEA analysis is done in detail for customers, and reports and suggestions are provided to customers to optimize product design. For some uncertain factors, we will suggest that customers do physical models for verification.
2. Software for analysis of mold design The structure of other parts of the product varies greatly. When engineers design the mold, they need to use the analysis software to simulate and analyze the computer, so as to avoid the design error entering into the mold manufacturing stage and causing serious losses. Both “Unigraphics” and “Pro / E” have some mold analysis functions. In addition, there is a separate professional mold analysis software “Moldflow”. A)."Moldflow" simulation software tool is a professional injection molding simulation tool, which can help you to verify and optimize plastic parts, injection mold and injection molding process. The software can provide guidance for designers, mold makers and engineers, and show how the wall thickness, gate location, material and geometry changes affect the manufacturability through simulation settings and results clarification. From thin-walled parts to thick walled, solid parts, Moldflow's geometry support can help users to test the assumptions before final design decisions. B) MAGMAsoft simulation software can simulate and analyze the mold filling, solidification, cooling, heat treatment, stress and strain in the casting process. The simulation technology of the software makes the complex casting process become digital and visualized, which is easier to be observed and understood by the foundry people, and increasingly accepted by the foundry people.
6.Process follow-up:
Follow-up in the manufacturing process is to ensure that mold processing in accordance with the norms, to avoid deviations from the guarantee. Each mold is a brand new product for designers and manufacturers. It is very necessary to find the faults in manufacturing and adjust and correct them in time.
Engineers should apply the acquired experience and methods to the subsequent mold design and manufacture.
As a professional manufacturer engaged in injection mold manufacturing and injection production for nearly 20 years, we have excellent engineer team and rich experience in manufacturing and injection molding. We can make high quality mold and products for our customers and provide thoughtful service.