Nylon part injection molding
Short Description:
Nylon part injection molding is mainly used for the production of engineering parts.Nylon products are widely used in automobile, electrical appliances, communication, electronics.
MESTECH has the injection molding machinery ranges in size from 90 to 1200 tons, allowing us to manufacture nylon plastic parts of many sizes and scales. We are happy to discuss nylon injection molding ideas and solution with each client to ensure the process and materials are an ideal fit for your project.
Nylon injection molding parts are used in many fields because of their excellent mechanical properties, such as gear pulleys, wheels, high voltage parts, cryogenic environment equipment, ultrasonic environment equipment, as well as replacing steel parts and aluminum parts for machinery and daily equipment.
What are nylon injection molded parts used for?
Nylon material is used in a large range of different industrial applications because of its impressive mechanical and electrical properties, excelling in toughness, wear resistance and chemical resistance. Nylon injection molding produces plastic parts that are used in countless industries and applications, such as:
Consumer apparel and footwear
Sports and recreation equipment
Industrial components
Medical products
Automotive products
Nylon is used for a variety of applications to include clothing, reinforcement in rubber material like car tires, for use as a rope or thread, and for a number of injection molded parts for vehicles and mechanical equipment. It is exceptionally strong, relatively resistant to abrasions and moisture absorptivity, long lasting, resistant to chemicals, elastic and easy to wash. Nylon is often used as a substitute for low strength metals. It is the plastic of choice for components in the engine compartment of vehicles because of its strength, temperature resilience, and chemical compatibility.
As nylon has great bending strength, it lends itself well for parts that will be intermittently loaded. Furthermore, with the high wear resistance and low coefficient of friction, nylon works well in applications such as slides, bearings and any device that is put through motion.
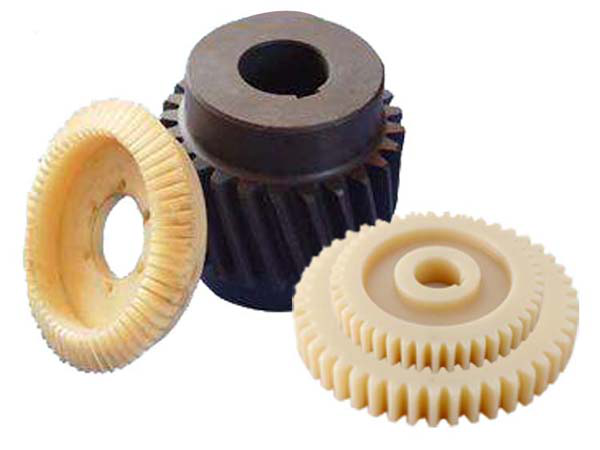
Nylon PA66 gear
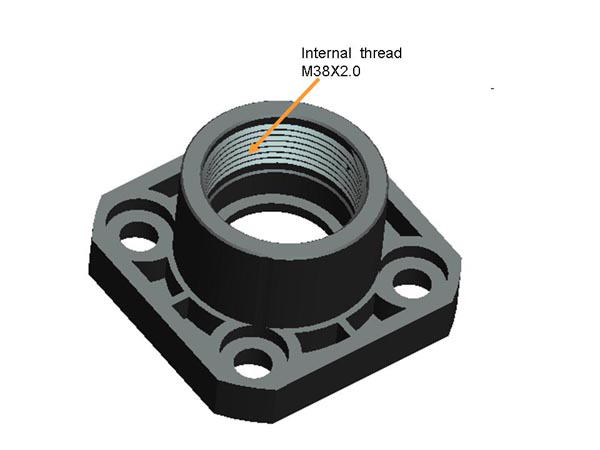
Internal thread nylon cover
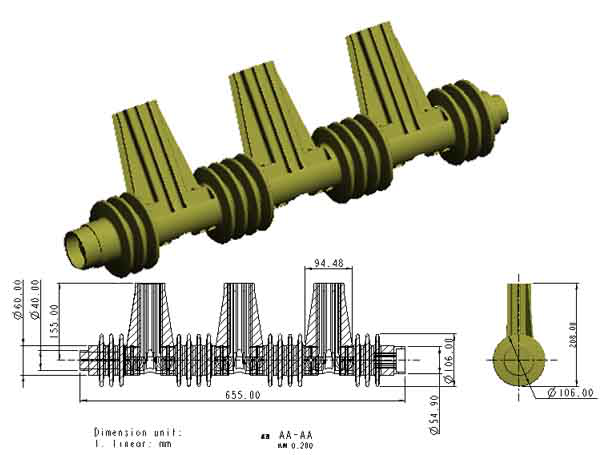
High voltage nylon switch shaft
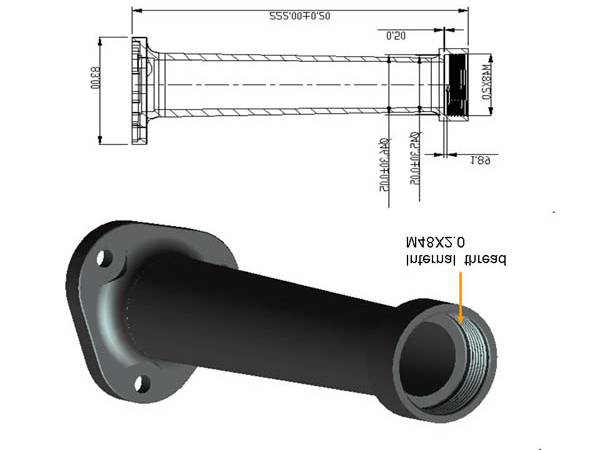
Long sleeve for electrical
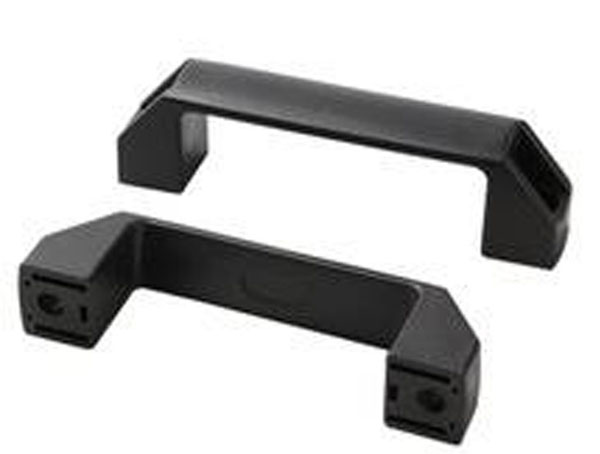
Nylon Doorknob
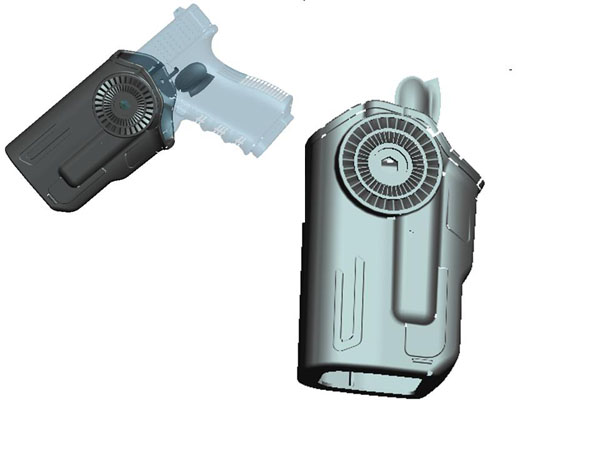
Nylon holster pister cover
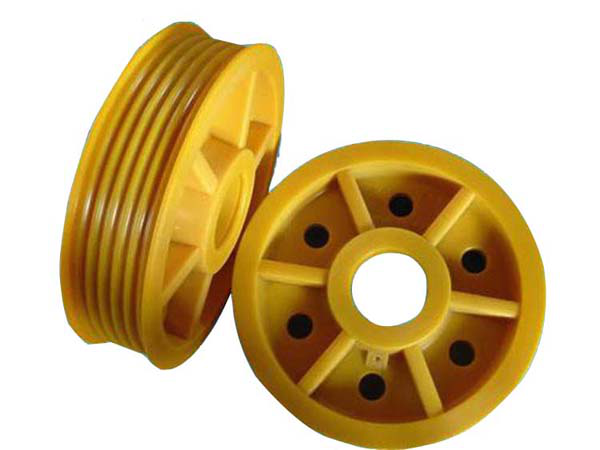
Nylon guide pulley
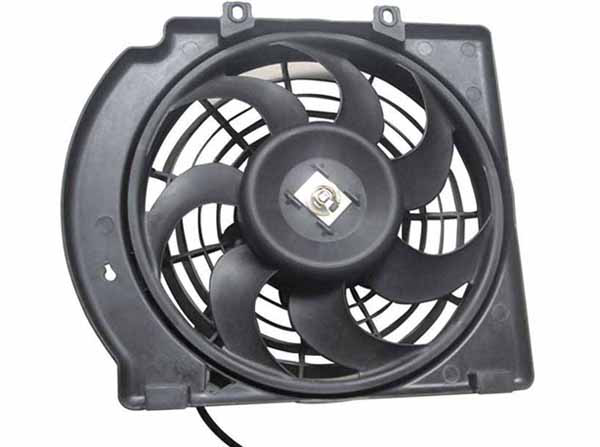
Automobile exhaust fan
What are the differences of the different types of Nylon
In the modern era it is manufactured by a large number of firms, each typically with their own production process, unique formula, and trade names. You can view a full list of material manufacturers here.
Common variants include Nylon 6, Nylon 6/6, Nylon 66, and Nylon 6/66. The numbers indicate the number of carbon atoms between acid and amine groups. Single digits (like “6”) indicate that the material is devised from a single monomer in combination with itself (i.e. the molecule as a whole is a homopolymer). Two digits (like “66”) indicate that the material is devised from multiple monomers in combination with each other (comonomers). The slash indicates that the material is made up of different comonomer groups in combination with each other (i.e. it is a copolymer).
Nylon can also be combined with a large variety of additives to produce different variants with significantly different material properties.
Do you know the tips for injection molding nylon ?
(1).Thickness design of walls or ribs
Nylon has high shrinkage and is sensitive to the wall thickness of parts. On the premise of guaranteeing the properties of products, the wall thickness should be as small as possible. The thicker the products are, the bigger the shrinkage is, and the strength is not enough, so the reinforcement can be increased.
(2).Draft angle
High shrinkage, easy demoulding, the draft angle of demoulding can be 40 ′ -1゜40′
(3).Insert
The thermal expansion coefficient of nylon is 9-10 times larger than that of steel and 4-5 times larger than that of aluminum. Metal inserts hinder the shrinkage of nylon and cause greater stress, which may lead to cracking. It is required that the thickness around the insert should not be less than the diameter of the insert metal.
(4).Hygroscopicity
Nylon is easy to absorb moisture and must be dried before forming.
(5).Mold venting
Nylon has low viscosity, and fills the mould quickly under high pressure injection. If the gas can not be discharged in time, the product is prone to air bubbles, burns and other defects. The die must have an exhaust hole or an exhaust groove, which is usually opened opposite the gate. The diameter of the exhaust hole is_1.5-1 mm, and the depth of the exhaust groove is less than 0.03 mm
Mestech is committed to making injection mold and injection molding production of nylon parts for customers. Please feel free to contact us if you want to now more.