Plastic prototype
Short Description:
For plastic products that need mold production, we usually do some physical plastic prototype to verify its design. It refers to one or several functional model that are made according to the product appearance drawing or structure drawing without opening the mold to check the rationality of appearance or structure. Plastic prototype in different places is also known as the plastic sample, model,mackup.
Plastic prototype is an important way to evaluate product design and display products. It is based on product design drawings, using machine tool processing or resin laser curing or bonding process to produce samples for evaluating design and display. When we design a new product, samples are usually made according to the product appearance or structure drawings to check the appearance or structure rationality of functional templates. Making prototype is one of the most effective ways to verify product design and reduce manufacturing risk.
With an aim to provide the most efficient method to manufacture your prototype and tool, our design engineers are here to provide you with a design for manufacture service to ensure your product(s) are always suitable for a plastic product manufacturer. Through thorough analysis and specific material selection, we can strengthen the confidence of your project and offer a rapid prototyping service to compliment the design – this provides ample opportunities for functionality testing which will highlight any possible alterations that need to be made to the design to best suit your market requirements. This ensures that product design issues do not enter the follow-up stage of mold production, to avoid late failure and huge cost waste. For large-scale industrial products, whether complex electronic products, electrical appliances, automobiles, medical instruments, toothbrushes, water cups and other simple daily necessities, in the product design stage, prototype sample should be made to evaluate and verify the technical feasibility, technological and market aspects, and constantly improve the optimization design. Get the best results.
Types and uses of plastic prototypes
1. Appearance prototype: At the beginning of the new product design stage, make the appearance prototype to evaluate and improve the different appearance layout of the product, and select the most reasonable and attractive appearance scheme for customers.
2. Structural prototype: After the product structure design is completed, normally the prototype is made according to the structural design drawing before the mold manufacturing. The designer checks the structure design prototype to find what defect in design in advance, and improve and optimize the design, so as to avoid the risk on manufacturing.
3. Functional prototype: In response to customer needs or market promotion needs, the prototype is pre-displayed to the market and customers before the mold is made or the mold is not completed.
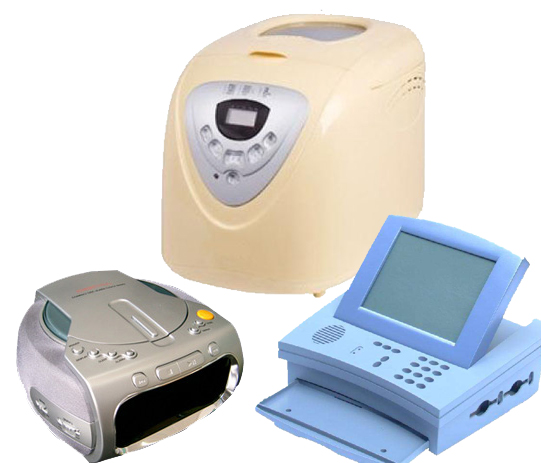
Appearance / Structural prototype
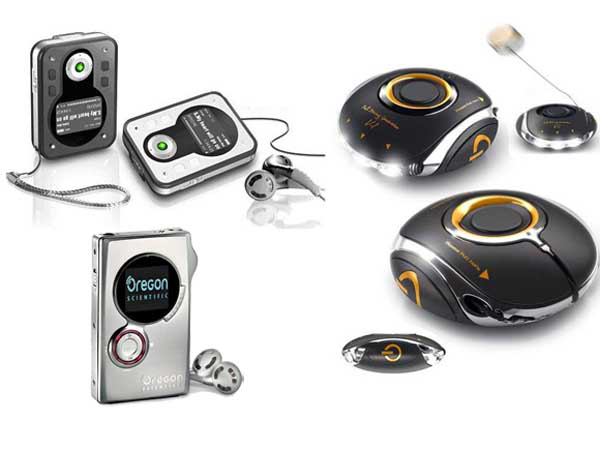
Functional prototype
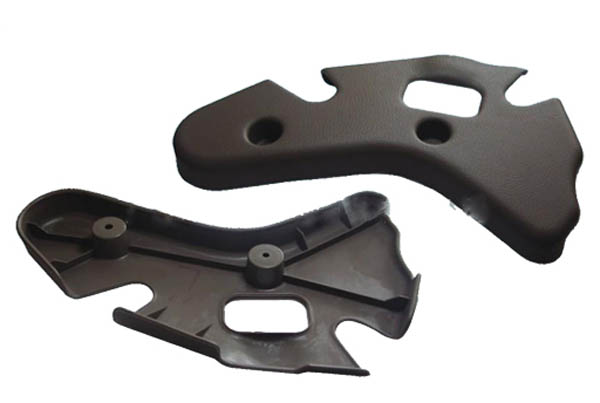
Structural prototype
There are five main technology to make plastic prototypes as following
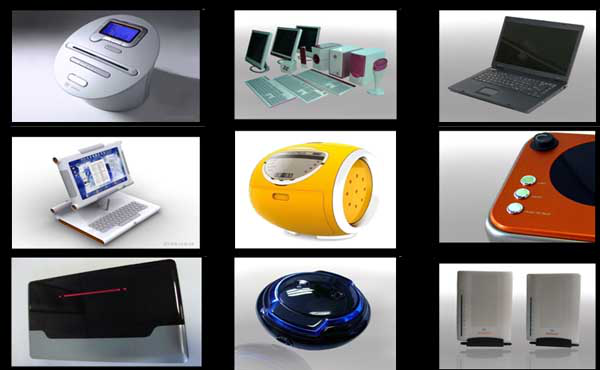
CNC Machining plastic prototypes
1. CNC Machining: The prototype is mainly produced by a cutting center. Referring to the product design drawing, the redundant material is removed from the solid plastic blank by cutting tool on the cutting machine tool, and the parts conforming to the size and shape are obtained. After CNC processing, some manual processing is generally needed.
---Advantage: parts can be made of various materials according to need; parts made have good precision, strength and no distortion; easy to obtain better surface quality, easy to paint, electroplating and screen printing. Suitable for samples with assembly matching, moving parts, large parts, parts with decorative appearance, and functional machines. Delivery time is 7-8 days. It is suitable for making appearance prototype, functional prototype and structural prototype.
---Materials: ABS, PC, POM, PMMA, nylon, etc.
---Disadvantage: The disadvantage is the need for a certain amount of manual processing, high cost. The more complex the structure, the higher the cost.
2. SLA or stereolithography Prototyping - SLA technology solidifies a single layer by laser scanning exposure. Through the ultraviolet laser beam, according to the designed cross section of the original layer, curing point by point, from point to line, from line to surface, through the movement of lifting platform, three-dimensional printing is completed by stacking layer by layer. The prototype was removed from the tank and stabilized under the ultraviolet lamp. Depending on the complexity, the delivery date can be as short as 2-3 days.
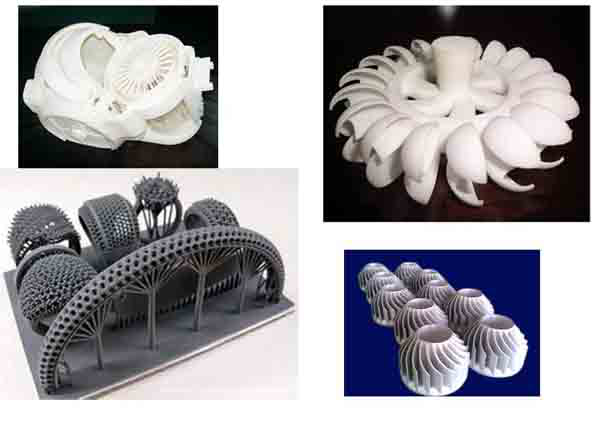
SLA plastic prototypes
3. SLS or selective laser sintering. This involves building components from 3D data using resin powders and lasers. Simulated injection grade can be used to provide some performance, including "movable hinge" components. Delivery date may be 2-3 days, depending on complexity. During the sintering process of SLS, the temperature of powder material (or its binder) has just reached the melting point, and it can not flow well and fill the gap between powder particles. Therefore, the surface of the part is loose and rough.
---Advantages: Good strength, not easy to deform, impact resistance, can withstand weight and a certain amount of machining. Easy to bond. Corrosion resistance. It is suitable for making structural prototype.
---Material: Using nylon powder, polycarbonate powder, acrylic polymer powder, polyethylene powder, nylon powder mixed with 50% glass beads, elastomer polymer powder, ceramic or metal and binder powder and other materials, performance comparison.
---Disadvantages: poor dimensional accuracy and surface quality. Used for structural prototype which high appearance quality is not required.
4. Vacuum prototype (Vacuum Filling) Vacuum reproducing is a way of making small batch models. It uses the original prototype (CNC prototype or SLA prototype) to make silica gel mould in vacuum, and uses PU material to pour in vacuum, so as to clone the same replica as the original prototype, which has better heat resistance, strength and hardness than the original prototype. If customers require several or dozens of sets, it is suitable to use this method, which greatly reduces the cost. 。 Materials can provide a variety of simulation materials to achieve some of the properties of injection moulding parts. Delivery date may be 7-10 days, depending on complexity.
---Advantages: It is necessary to use CNC or SLA process to make original sample, which is suitable for several sets to dozens of sets of small batches of samples. Size stability, strength and toughness are higher than SLA prototype, close to CNC prototype. It is suitable for making appearance prototype.functional prototype and structural prototype.
---Material: PU resin is generally used, but also can provide a variety of simulation materials.
---Disadvantage: Not suitable for parts with complex shape. The price is lower than that of CNC samples.
5. RIM (Reaction Injection Moulding) is also the use of the original prototype (CNC prototype or SLA prototype) made of silica gel mold, the liquid two-component polyurethane PU is injected into the rapid mold at room temperature and low pressure environment, curing and post-processing to obtain the required plastic samples.
---Advantages: It is used for small batch replication of simple and larger panels and production of large thick-walled and non-uniform wall thickness products. It has the advantages of high efficiency, short production cycle, simple process and low cost.---Material: Two-component polyurethane PU.
---Disadvantage: The materials used are single.
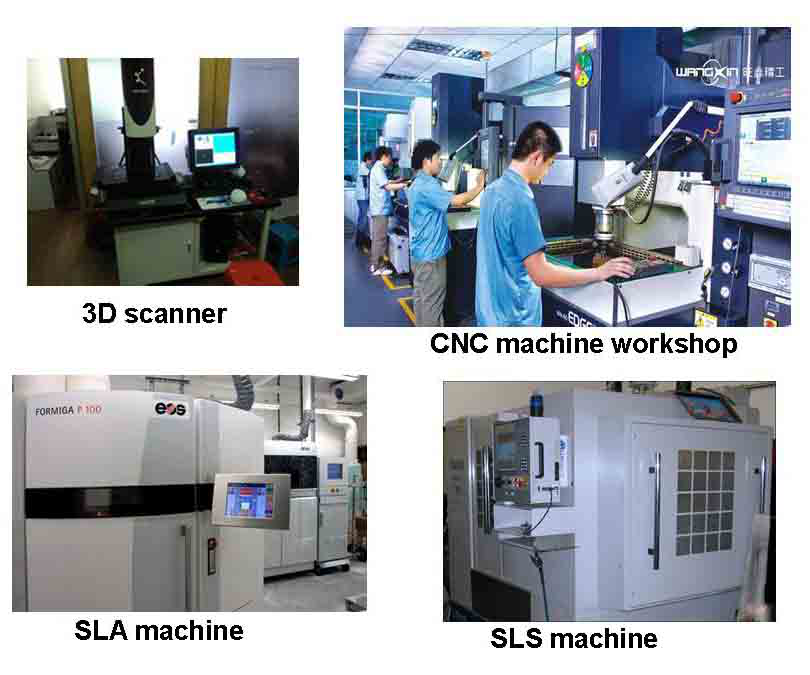
Prototype surface treatment: polishing, painting, silk printing, gilding, electroplating.
Each rapid prototyping process can offer a variety of post-mould finishes and painting techniques, in order to create a professional look. At this stage, our engineers can recommend further rapid prototyping tooling options to achieve a more aesthetically pleasing and functional product. As a one-stop service, we provide you with a series of services, such as product design, prototyping, mold processing and injection molding, machining, and product assembly. It is one of the tasks to provide you with prototype samples of plastic and metal parts. In your product development cycle, with our full assistance, we can ensure that your products enter the market in a fully functional and cost-effective manner.
Prototype evaluation is an important part of product design. Mestech also offer product design, mould tooling, plastic injection molding and product assembly services to further support your manufacturing process.