Tips for precise plastic parts design and molding
Short Description:
Precision plastic parts design and injection molding should start in materials, parts structure design, mold design and processing, injection molding machine , professional operation and good production environment.
With the development of modern industry, there are more and more excellent plastic materials. At the same time, plastic products are also widely used in various industries. Especially, more and more precise plastic parts are used. Now let's share with you the tips for precise plastic parts design and molding.
Classification of precision
plastic parts :
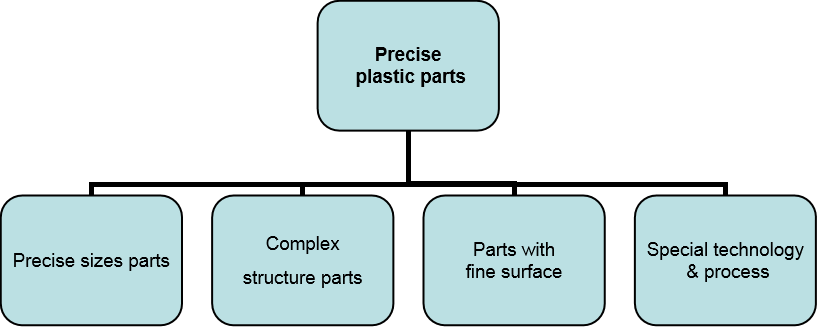
1. Design of precise plastic parts
(1) Typical types of precise plastic parts
A. High dimensional accuracy parts, such as: motor gears, worm gears, screws, bearings. These precise parts are usually used in the precise transmission mechanism of machines (such as printers, cameras, automatic vacuum cleaners, robots, smart appliances, small UAVs, etc.). It requires precise coordination, smooth movement, durability and noise-free.
B. thin-walled parts:
Usually, the wall of plastic parts is less than 1.00mm, which belongs to thin-walled parts. Thin-walled parts can make the size of the product very small. But plastic thin-walled parts can hardly be filled because of the rapid cooling and solidification. And the thin-walled parts can not withstand the force of the die and break in the die cavity. Therefore, the design of thin-walled parts should choose materials with better mechanical properties. And reasonable design, such as uniform wall thickness, parts can not be too wall. Deep die, larger angle. For some ultra-thin parts, high-speed injection molding machine is needed.
C. Optical parts:
Optical parts require good transmittance/light diffusion performance, as well as good dimensional stability and wear resistance. For example, the surface curvature of concave and convex lenses used in projectors requires high accuracy and stability. High transparent plastic such as PMMA is needed. At the same time, some lighting optical parts also need to do some fine lines on the surface of the parts to accept light or even light or eliminate glare.
D. High-gloss surface:
High-gloss parts include optical parts, as well as other parts requiring high surface finish (mirror surface). This kind of parts are widely used in consumer electronics products, such as mobile phone shells. The design of this kind of products should consider plastic materials with good fluidity, thickness design and die technology.
E. waterproof plastic parts
Many electronic and electrical products require water-proof, such as waterproof glasses/watches/military electronics, outdoor products and instruments with damp water environment. The main methods of waterproofing are encrypted seals on the outer surface of the product, such as enclosed keys, enclosed jacks, sealing grooves, ultrasonic welding, etc.
F.IMD/IML (in-mold-decoration, in-mold-label)
This process is to place the PET film in the injection mold cavity and integrate the injection parts into a whole processing technology, which will stick firmly to the plastic parts. IMD/IML products features: high clarity, stereoscopic, never fade; transparency of window lenses as high as 92%; wear-resistant and scratch-resistant surface for long service life; buoyancy of key products during injection moulding, key life can reach more than 1 million times.
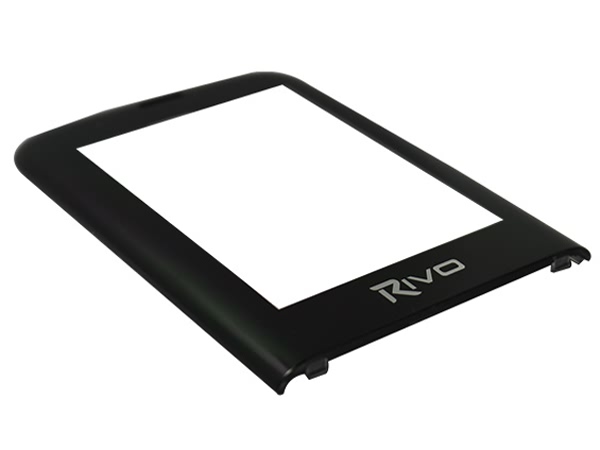
Thin wall plastic part
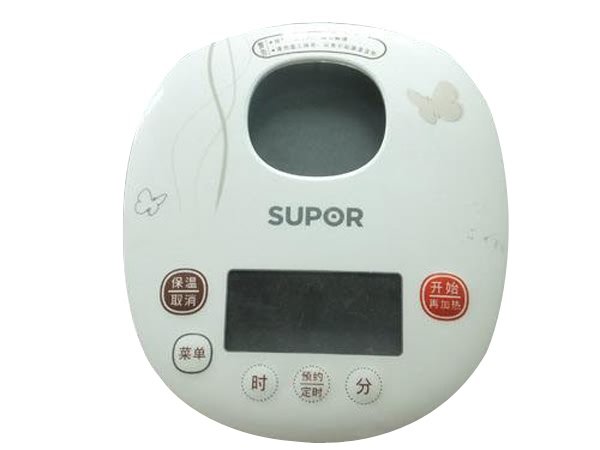
IMD/IML plastic panel
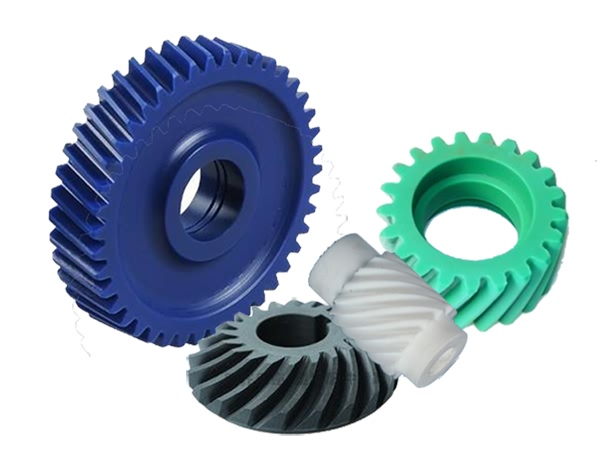
Precise plastic parts
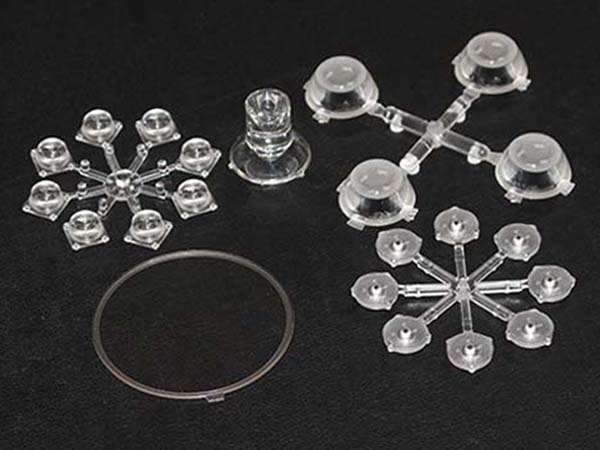
Optical part / transparent cover
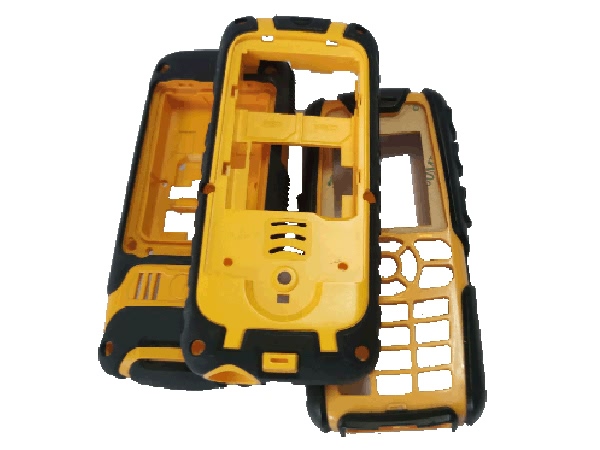
Double injection waterproof case
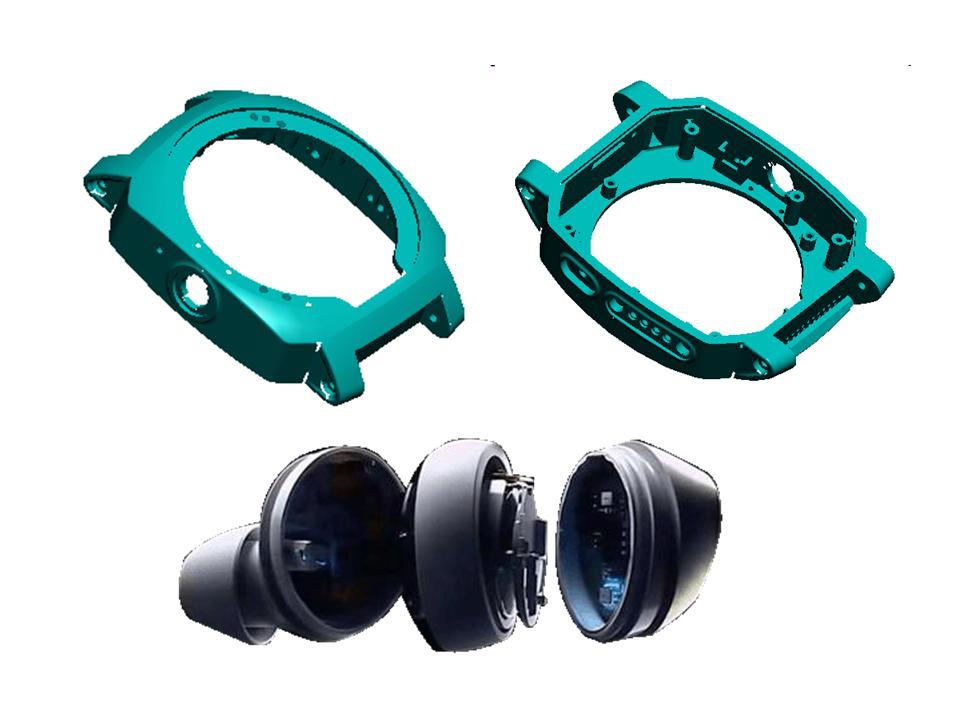
Precise case for electronic products
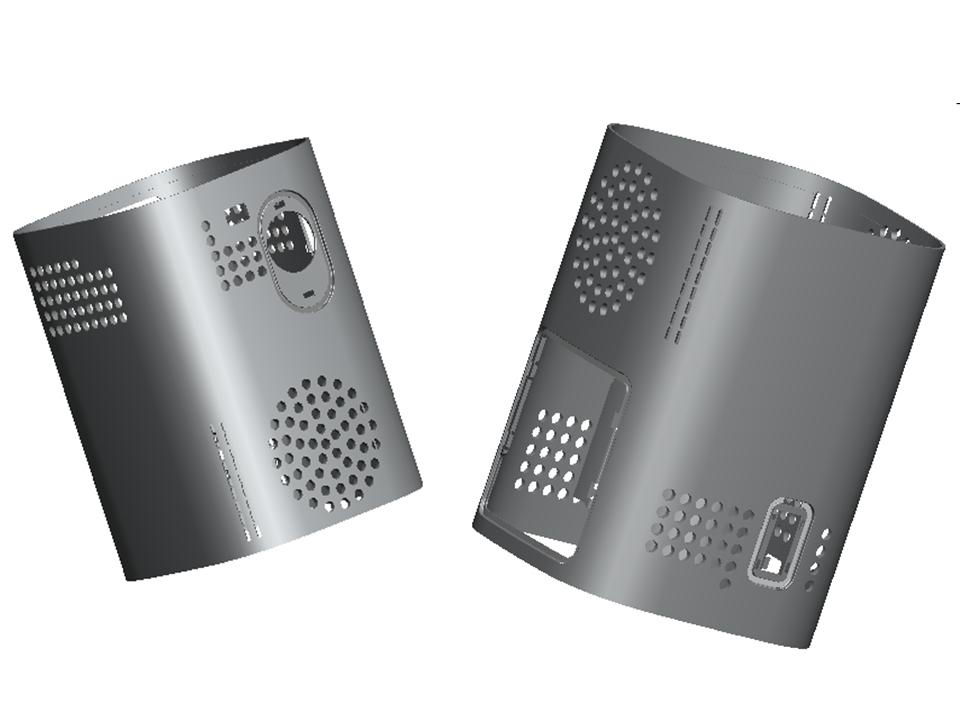
Porous housing of complex structure
(2).Tips for precise plastic parts design
A. uniform wall thickness In injection moulding, the plastic is in liquid state for a very short time, and the uniformity of the wall thickness of the parts has a great influence on the flow velocity and direction of plastic. The thickness of the parts changes greatly, which will bring a series of quality defects such as filling dissatisfaction, deformation, shrinkage, weld marks, thick and thin stress marks, etc. Therefore, the wall thickness of precise plastic parts should be as uniform as possible in design. The thickness change should not be too large, and slope or arc transition should be made in the change.
B. pay attention to the coordination between parts and make suitable size accuracy requirements. In order to ensure the interchangeability between parts, we often give strict requirements for the accuracy of individual parts. But for plastic parts, it has certain flexibility and elasticity. Sometimes, as long as the structure design is reasonable, the deviation can be corrected by the interaction between parts, so the accuracy standard can be relaxed appropriately to reduce the manufacturing difficulty. Degree.
C. material selection There are many kinds of plastic materials, and their performance varies greatly. For precise plastic parts, materials with small shrinkage/deformation/good dimensional stability/good weather resistance are selected according to the requirements of use. (a)ABS/PC with low shrinkage is used to replace PP with high shrinkage, and PVC/HDPE/LDPE with low shrinkage. ABS+GF is used to replace ABS.PC+GF with PC. (b)Choose PA66+GF or PA6+GF instead of POM or PA66 and PA6.
D. fully consider the molding process.
(a) For ordinary thickness shell, box or disc parts, it is better to design microstrip arc on the surface and reinforcement on the interior to avoid deformation.
(b) For ultra-thin parts, the thickness of the parts should be uniform, and the inner parts should not have deep reinforcing ribs or complex structures. It is recommended to use high-speed injection moulding machine.
(c) Hot nozzles or hot runner moulds are used for large parts to prolong filling time and reduce forming stress and deformation.
(d) for two-component parts made of two materials, double color injection instead of glue injection is adopted.
(e) vertical injection molding is recommended for parts with small metal inserts.
E. Has room for improvement. In the design of precise plastic parts, it is necessary to assess possible deviations in future production.
(3) Design verification
Injection moulds have high cost, long time and high cost of modification, so after the basic completion of part design, it is necessary to make physical samples to verify the design, in order to determine the rationality of product design parameters, find problems and improve in advance.
The design of physical verification is mainly accomplished by making prototype model. There are two kinds of prototype making: CNC processing and 3D printing.
The use of prototypes physical verification requires attention to the following aspects:
A.CNC prototype production costs are generally higher than 3D printing. For large parts, the cost of CNC processing is relatively low.
For materials and mechanical properties or surface treatment and assembly requirements, CNC processing is recommended, so that good mechanical strength can be obtained. For small size and low strength parts, 3-D printing is used. 3-D printing is fast, and it is much cheaper for small size parts.
B. Prototypes can generally verify the assembly matching between parts, check design errors and omissions, and facilitate design improvement. However, prototype can not generally reflect the technological requirements of mold forming, such as molding draft angle/shrinkage/deformation/fusion line and so on
2. precise plastic parts molding
(1) plastic mold design (mould design) High quality molds are the key to making precise parts. The following points need to be followed.
A. accurately select the shrinkage coefficient of plastic material. Reasonable position of parts in the mold.
B. mold core material shall be selected as steel material with good stability / wear resistance / corrosion resistance.
C. mold feeding system uses hot Tsui or hot runner as far as possible, so that parts of each part of the temperature uniformity, reduce deformation.
D. mold must have a good cooling system to ensure that parts are cooled evenly in a short time.
E. mold must have side lock and other positioning devices.
F. reasonably set the ejection position of ejector mechanism, so that the ejection force of parts is uniform and not deformed.
Mold design and analysis important tool (moldfow): Using the simulation software of injection moulding to imitate the effect of injection moulding process under different setting parameters, find out the defects in product design and mould design in advance, improve and optimize them, and avoid the major mistakes in mould manufacturing to the greatest extent, which can greatly ensure the quality of the mould and reduce the later cost.
(2) verify mold.
The cost of simple mold is much lower than that of production mold. For precise injection plastic parts, it is necessary to make a simple mold to verify the design of the mold before making the formal production mold, so as to obtain parameters to improve the design of the mold and ensure the success of the production mold.
(3) mold processing
High quality molds must be machined with the following high precise machines.
A. high precise CNC machine tool
B. mirror sparkle machine
C. slow wire cutting
D. constant temperature working environment
E. necessary testing equipment. In addition, mold processing must follow strict process and rely on high-quality staff to operate.
(4) injection molding machine selection
Equipment for injection molding of high precise plastic parts.
A. should use precise injection molding machine with no more than 5 years of service life.
B. factory environment is clean and tidy.
C. for ultra-thin parts, there must be a high-speed injection molding machine.
D. double color or waterproof parts must have two color injection molding machines.
F. sound quality assurance system
(5) packing for precise plastic parts
Good packaging is important to prevent scratches, deformations,dust in the transportation, storage of precise plastic parts.
A. high gloss parts must be pasted with protective film.
B. thin-walled parts must be wrapped in special pockets or foam, or separated by paper knife to avoid direct pressure.
C. Parts that need to be transported over long distances should not be placed loosely in cartons. Multiple cartons should be fixed together by stacks and guards.
Mestech company has machines and equipment for making precise plastic mold and injection molding production. We hope to provide you with mold making and production services for precise plastic parts.